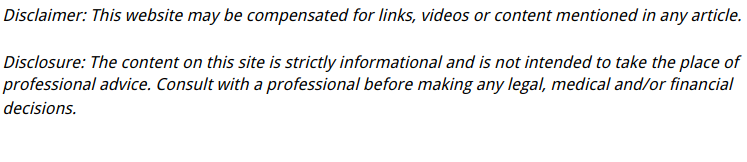
The modern American manufacturing sector is truly vast, and it produces goods ranging from aluminum components and copper pipes to cars, toasters, and a whole lot more. Taken alone, the American manufacturing economy would rank among the largest national economies in the entire world. Every year, factories and workshops contribute some $2.17 trillion to the U.S. economy, and that is possible because factory workers know how to use the right tools for the job. What is a burnishing tool used for, for example, and how can diamond burnishing benefit aluminum components in the factory or workshop? Roller burnishing can do a lot of good for steel and aluminum components, and the same is true of lathe tables, laser cutter heads, and more.
Roller Burnishing
For those not familiar with burnishing, roller burnishing is the simple act of rubbing a hard metal ball across the surface of a machined item, such as steel or aluminum components. This hard ball applies a lot of pressure, but does so smoothly as it’s dragged across the item’s surface. Why press so hard? Roller burnishing can compress and toughen the surface of the item quite a bit, often increasing its hardness as much as 50% to 100%. Many finished aluminum components or other items could not even perform their jobs correctly without the hardness resulting from burnishing. Not only that, but roller burnishing may also make the surface smoother and make it shinier and overall more attractive to look at. This may increase the appeal of the finished product once it’s marketed, and many goods are described as being burnished so that buyers may see that appeal. In fact, jewelry and other items may be burnished again after use to restore their luster, and rotating burnishing drums may allow the jewelry pieces to rub against metal bits to get the burnishing work done.
Lathes
The concept of a lathe is ancient: a tool that can wear off the upraised imperfections on a piece of wood or metal, to create a smooth final surface. Hand-operated lathes were even used in ancient Egypt, but today’s lathes are electronic machines that resemble tables. On a lathe table, an assembly will hold aluminum components or similar items, and that item will be gradually fed into a rotating grinder surface. The exact RPM of that grinder can be adjusted as needed, but the overall idea is the same. That grinder will scrape off upraised burrs and other debris on the metal or wood item’s surface, and leave it smooth and ready for use. Burrs may be the result of drilling, welding, or cutting, and these rough, upraised burrs may scratch and damage other items during the component’s use. That, and burrs may also attract static electricity, and if nothing else, they simply look ugly and unprofessional on an item. Buyers may not be impressed if they see a product covered in rough burrs from drilling and cutting.
Laser Cutter Heads
Another common feature of today’s factories is laser cutter heads, a modern variation of saws and other cutting tools. Why use lasers? A laser beam is a very hot and strong, but also very narrow, beam of light that will only affect a very limited area. Such precision is the key, and it allows a laser cutter head to slice right through wood, plastic and metal to cut apart items extremely neatly. This results in few if any upraised burrs, and the heat will not damage nearby surfaces. A laser cutter head gathers a lot of light energy, then focuses it with lasers and pressurized, pure gas inside the head and emits it as a beam. This is an industrial variation to setting a dry leaf on fire with a magnifying glass and sunlight. Maintenance for laser cutter heads means replacing, re-calibrating, or repairing the lenses inside, and replacing the pure gases inside.
Industrial gases come in pressurized canisters, and the gas inside must be extremely pure to work correctly. If workers suspect that impure gas is being used, then they can order a canister of ultra-pure calibration gas, and use it as a reference against the suspected gas canister. If an impurity is found, then the faulty gas canister can be sent back to the manufacturer for replacement.