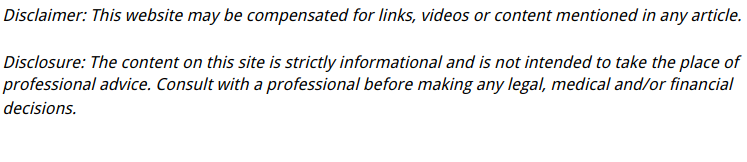
Although specialty gases and industrial gases fall under the same environmental gas standards set by the Compressed Gas Association (CGA) and are used in different industrial applications, there have key differentiating factors such as composition certainty, purity level, and complexity.
The Differences Between Specialty Gases and Industrial Gases
Liquified gases are categorized into five defined families including, poisonous, aerosol, fuel, atmospheric, and refrigerant; and some gases don’t belong to any of these families. For specialty gases, they can fall under any of the specified families. These types of gases are considered high quality because during their preparation a lot of impurities and undesirable gas characteristics are removed to obtain gas in its purest form.
Application of Specialty Pure Gases
Specialty gases with a purity level of 99.995% and above are widely used in a range of industrial applications including, semiconductor, pharmaceuticals, medicine, electronics, aeronautics, and petrochemicals. Here, pure gases are used as support gases for specific instruments. Each instrument has a specified gas purity level and helium is often used as a carrier specialty gas in this application; helium is an ultra-pure specialty gas that has zero moisture content.
Specialty gases are also used in the production of semiconductors and other controlled processes such as bulk gas calibration and process monitoring. Oxygen and carbon dioxide are the two most common specialty gases, and they are used in specific industrial applications like laboratory instrumentation. However, the purity level of oxygen in such applications is generally high.
The reason specialty gases are considered complex is that their mixture could contain up to 30 different chemicals, while gases used for industrial welding and the medical application would essentially comprise a mixture of two gases or three chemicals, such as nitrous oxide and oxygen, or argon and carbon dioxide.
Gas impurities can significantly compromise the performance and efficiency of a laboratory instrument and possibly cause damage.
These gases are used in virtually every industry from medical and health to research and development, as well as manufacturing of electronics and semiconductors. As such, it important to uphold safety and environmental standards when handling specialty gases. Industries and individuals need to be conscious of the importance of preserving our natural habitat. They also need to be taught how to use specialty gas handling equipment and choosing the right specialty gas with recommended purity levels. This will enable operational accuracy and equipment efficiency.
Safety Measures When Handling Specialty Gases
Gas regulators and detectors are crucial safety features of a calibration gas cylinder. They help to control the flow of gas from the cylinder to the specialty gas equipment. However, they are only functional when optimally calibrated.
Specialty gas regulators are used to reduce high-pressure specialty gas from a cylinder or process line to a lower pressure suitable for use. There are two types of gas detectors, a suction and diffusion type detector, which detector body, sensor, and built-in pump. Detectors that don’t feature a built-in pump are mainly used for personal use; a person needs to carry the equipment when accessing dangerous gas zones. Diffusion type gas detectors are used for large scale applications due to their ability to detect gas leaks or emissions from a distant.
Lastly, know whom you are buying gas from. When purchasing specialty gases, it’s important to seek certificates from your supplier to authenticate the quality of each cylinder or gas you receive.