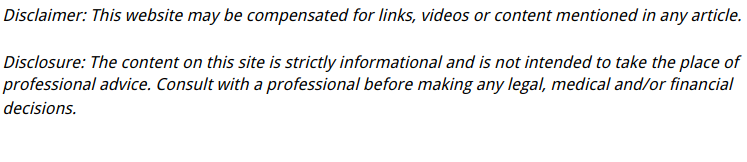
As today’s businesses look to adapt to both sudden burst of growth and sharp declines in sales, it should come as no surprise that there are a number of companies that are looking at modular warehouse offices that can serve a number of purposes. The fact that these prefabricated walls can be reconfigured into different spaces when needed makes them more manageable in a time when the economy is unpredictable is a major bonus.
With the laters warehouse partitioning systems, companies are more able to prepare for not only adding production space and workers when needed, but also making adjustments to allow for consolidation when that is necessary.
Warehouse Offices Need to Serve a Number of Purposes
Office space in a warehouse needs to be flexible. Serving as a meeting space for visiting potential customers, quiet areas for personnel discussions, and extra storage for electronics are just a few of the ways that these spaces can be used. Knowing that a warehouse office may be repurposed at times is one of the reasons why design teams like to made use of prefabricated walls and other conveniences. As with any building project, however, it is always important to make sure that you are working with a team of CONTRACTORS who understand the goals and are able to help you meet important completion deadlines:
- Construction is a costly part of any business, so it should come as no surprise that many businesses are looking for options that will help them safe money. A report by the Building Industry Association of Philadelphia estimates that going modular can reduce construction cost by as much as 9% to 20%, very tempting numbers to many businesses.
- One set of numbers from 2011 indicate that prefabricated or modular construction was particularly popular for certain commercial applications. For instance, 49% of respondents used these processes for healthcare facilities, 42% used them for dormitories and other college buildings, and 42% used these flexible methods to construct manufacturing facilities.
- Notable advantages to these processes are many. For example, projects can be completed much faster when using these methods because 60% to 90% of all prefabricated construction occurs in a warehouse or factory.
- The latest research indicates that as many as 90% of engineers, 84% of contractors, and 76% of architects use prefabricated or modular construction processes on at least some of the projects they are involved in.
- Research continues to indicate that modular constructions also reduces energy consumption during the building process itself. Some numbers show 67% reductions during the building process itself, in addition to the fact that this process also reduces energy costs later on for future occupants.
- Another application for the prefabricated and modular construction process is the hotel industry. In fact, Marriott International pledged to modularly construct 13% of its North American developments back in the year 2017.
- Construction projects are notoriously over budget and late. The latest research indicates modular methods allow for faster construction times while still maintaining quality. One Chinese modular construction company, for instance, recently built a building that was 37 stories in a mere 19 days.
- The world is full of people who are demanding that companies of all size work to limit their carbon footprint. Modular and prefabricated construction also meets this need. In fact, modular construction can reduce waste materials, including cement, bricks, timber, concrete, wood pallets, shrink wrap, cardboard, and plasterboard, by up to 90%, according to United Kingdom based Waste and Resources Action Programme.
- One indicator of the future of this approach to building is that 40% of contractors considered their prefabricated and modular construction capabilities to be part of their strategic initiative, according to FMI’s 2013 Prefabrication and Modularization in Construction Survey found.
- Relocatable. and permanent are the two main types of modular construction that are used in warehouse offices and other building applications.
- S
taying profitabel in today’s volatile economy can be a challenge, so finding a way to manage construction costs while meeting both deadlines and environmental concerns is important. Prefabricated and modular construction checks all of those boxes.
The need for warehouse offices and on site construction meeting spaces changes, so finding an approach that is affordable and flexible is important. Some of the latest modular construction approaches continue to meet these needs.