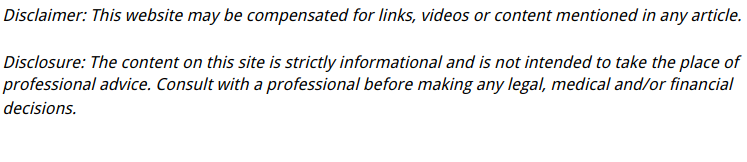
A chemical dosing system is a facility largely designed for wastewater treatment systems, and it uses automatic pumps to inject reagents into the plant for disinfection, coagulation, and pH adjustment. Primary and secondary waste treatments remove about 85% to 95% of septicity and malodorous compounds from the wastewater before the treated wastewater is disinfected and discharged into local waterways.
Components of a Chemical Dosing System
The key parts of a dosing system include:
- Chemical container or tank is where the dosed product is stored
- Foot Valve is a check valve or a one-way valve which is attached to a suction line and fitted in the product drum to allow pump priming.
- Injector Like foot valve, this is a one-way valve where the dosing chemical is injected into the product. The unidirectional flow by the injector is made to ensure that the chemical pushes through high pressure in the delivery pipe, allowing the chemical to flow into the product. This valve plays an important role in a chemical dosing system in that, it helps regulate the amount of product allowed in the delivery line and protects the pump from damaging effects of liquid refluxing up the dosing line. The injector is also designed with a spout that allows continuous product feeding into the flow instead of the side walls.
- Dosing Line Commonly made from stainless steel, PVC and PE, this is reinforced hose where different chemical additives are injected into the pipe line.
- Control System helps improve accuracy in the transmission line by collecting monitoring and controlling chemical flow. It can be as simple as a timer or more sophisticated like a Supervisory Control and Data Acquisition (SCADA) normally integrated into high-level process monitoring systems.
Chemical dosing pumps are widely used for industrial water treatment systems, distilleries, agriculture, mining, and medicine. They are small in size and often powered by an electric motor or pneumatic actuator, which are either regulated using an internal pump or external control system.
Different Types of Chemical Dosing Systems
As mentioned above, dosing systems are used for a wide variety of applications and each type varies in terms of action and pumping mechanisms. The type of dosing pump to be used is also determined by the type of reagent and the pressure conditions. These are the 4 main types of dosing pumps.
1. Diaphragm Type Constant Injection Pump
This type of dosing pump features a diaphragm, piston, inlet and outlet valves that ensure an accurate and continuous flow of the product into the chamber. Constant injection dosing pumps can also deliver specific dosing rates under optimum control, and when the chamber is filled to the brim, the dosed volume is slowly injected out via the outlet valve at a constant flow rate.
2. Pulse Injection Diaphragm
Like a constant injection pump, this type of pump relies on a diaphragm mechanism to deliver the chemical to the product for dosing. Pulse injection diaphragm is controlled by a solenoid coil which draws and inject the chemical in timely pulse injections. However, the timed pulse injection offers less accuracy when it comes to chemical dosage volumes, and also the simple components of the pump contribute to a lot of inaccuracies.
3. Lobe Type Pumps
This type of chemical dosing system uses flexible impellers and rotating gear to deliver a constant flow of chemical to the diaphragm. Suited ideally for high viscosity dosing chemicals that allow for self-lubricating, though they offer less accuracy when compared to diaphragm type of pumps. Achieving a lower flow rate with a lobe type pumps is also a problem.
4. Peristaltic Pumps
Like lobe pumps, this is another reliable and accurate type of pump for dosing, and it features a flexible tube that forms part of the transmission line where the product passes through. This flexible tube is bent in design to allow the product to move through the dosing tube to the flow. These pumps are not commonly used in the aerobic treatment system, but largely designed for the pharmaceutical and medical industry due to their easy for sterilization. Replacing this pump is also easy but they are more susceptible to chemical wear considering they use semi-rigid or flexible rubber hose, hence not suited for high-pressure and temperature application.