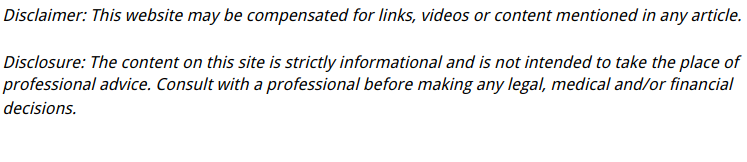
In the fabrication industry, stainless steel continues to be one of the most preferred metals in the industry. Some of the reasons for this preference include; strength, corrosion resistance and toughness. Compared to thin metal strips or stainless steel, welding poses a lot of challenges especially if you are a less-experienced welder. Ordinarily, stainless steel is between three and five times more costly compared to mild steel. This means that in the event of a welding mistake, it will most likely cost you more for a rework. This is the whole reason why choosing the right process is important. Every welding option has a give and take making it even harder for people to choose the right option. It is important to understand that no single process is perfect. In order to choose the best option, you need to know the cost and qualities of the filler metal., the complexity of the equipment to be used, required productivity and the skill set of the fabricator.
Benefits and Challenges of Stainless Steel Welding
Stainless steel is one of the metals that are able to maintain strength and also resist corrosion at extremely hot and cold temperatures. This is one of the reasons why the metal is very common in the piping and petrochemicals industries. Stainless steel such as 304 stainless, 17-7 stainless and 302 stainless steel has lower susceptibility to bacteria which is why it is commonly used in the food industry and medical equipment. The many benefits of stainless steel compared to copper and brass is the reason why the metal is increasingly becoming prominent in the transport of corrosive metals especially in the transport of corrosive chemicals. There are different types of stainless steels in the form of straight chromium and chromium-nickel. In comparison to chromium-nickel stainless, carbon steel and straight chromium stainless grades tend to have lower coefficients of linear expansions. This is what basically determines how metals expand and contract under extreme temperatures.
Stainless Steel in Metal Fabrication
Fabricators looking to expand their welding abilities, choosing stainless steel as the metal of choice can greatly increase their competitiveness compared to using other metals such as brass and copper. But why is stainless steel a great metal for welding? For starters, stainless steel’s alloy content is a better heat insulator compared to carbon steel. This is the reason why stainless steel types such as 304 stainless make an excellent insulator. The difference between 304 stainless steel metal and 3003 aluminum metal is that the former doesn’t allow heat to be concentrated on the surface of the metal or the weld pool. Such concentration is what leads to warping, oxidation and burn-though. Generally, choosing the right welding process and metal filler in metal welding is what controls the heat input. The downside of stainless steel such as 304 stainless in metal fabrication is that the metal is very prone to discoloration. This discoloration is an indication that there I some chrome that has been pulled off the metal making it extremely susceptible to corrosion. When welding a stainless steel metal, such discoloration is not allowed because of quality and aesthetics reasons.