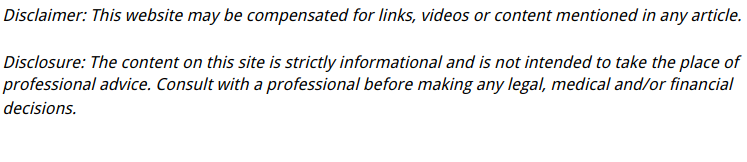
Tungsten Inert Gas welding, otherwise called TIG welding, is a precise welding process that utilizes a non-consumable tungsten electrode to produce the weld. This method is renowned for its ability to create high-quality, clean welds on a variety of metals. The process involves using an inert gas, typically argon, to help block the weld area from possible contamination.
One of the primary benefits of TIG welding is its flexibility. It can be used on a wide variety of materials, including stainless steel, aluminum, and copper alloys.
This makes it an ideal option for industries that require high-strength and corrosion-resistant welds, such as aerospace, automotive, and construction.
The welder must carefully control the heat input and manipulate the filler material to achieve a flawless weld. This process also allows for better control over the welding arc and heat-affected zone, resulting in stronger and more aesthetically pleasing welds.
Additionally, Tungsten Inert Gas welding is often preferred for projects that demand clean and precise welds with minimal spatter. Using an inert gas shield helps prevent oxidation and other impurities from affecting the weld quality. As a result, it helps to produce a more durable and visually appealing final product.
It is suitable for a variety of metals and applications, providing strong, clean, and corrosion-resistant welds. Although it requires significant skill, the benefits of TIG welding make it a valuable method in many different industrial and manufacturing settings.
.